Hello LS forum, 92' LS4 on craiglist and I bought it.
#151
Lexus Test Driver

3UZFTE,
What do you plan to weld with it? Aluminum, stainless, steel? TIG welding is an art. I know a guy in the business that can TIG weld aluminum and make it look like it was done by a machine. He worked for himself for many years but eventually went to work for an aerospace company, welding aircraft parts.
From a previous life, I have unlimited certification for plate welding, high pressure steam pipe up to 24" in diameter and natural gas line up to 18" in diameter. I've set up the steam and gas lines in whole production plants, manufactured and erected the structural steel in buildings up to around 14 stories, plus done a bunch of custom ornamental iron work. I also have a patent on a product that's made from steel and concrete. It's been installed in buildings up and down the east coast from NH, to FL., Including at Fenway Park in Boston, MA...
You can do a lot with a welder!
Jim
What do you plan to weld with it? Aluminum, stainless, steel? TIG welding is an art. I know a guy in the business that can TIG weld aluminum and make it look like it was done by a machine. He worked for himself for many years but eventually went to work for an aerospace company, welding aircraft parts.
From a previous life, I have unlimited certification for plate welding, high pressure steam pipe up to 24" in diameter and natural gas line up to 18" in diameter. I've set up the steam and gas lines in whole production plants, manufactured and erected the structural steel in buildings up to around 14 stories, plus done a bunch of custom ornamental iron work. I also have a patent on a product that's made from steel and concrete. It's been installed in buildings up and down the east coast from NH, to FL., Including at Fenway Park in Boston, MA...
You can do a lot with a welder!
Jim
#153
Instructor
Thread Starter

3UZFTE,
What do you plan to weld with it? Aluminum, stainless, steel? TIG welding is an art. I know a guy in the business that can TIG weld aluminum and make it look like it was done by a machine. He worked for himself for many years but eventually went to work for an aerospace company, welding aircraft parts.
From a previous life, I have unlimited certification for plate welding, high pressure steam pipe up to 24" in diameter and natural gas line up to 18" in diameter. I've set up the steam and gas lines in whole production plants, manufactured and erected the structural steel in buildings up to around 14 stories, plus done a bunch of custom ornamental iron work. I also have a patent on a product that's made from steel and concrete. It's been installed in buildings up and down the east coast from NH, to FL., Including at Fenway Park in Boston, MA...
You can do a lot with a welder!
Jim
What do you plan to weld with it? Aluminum, stainless, steel? TIG welding is an art. I know a guy in the business that can TIG weld aluminum and make it look like it was done by a machine. He worked for himself for many years but eventually went to work for an aerospace company, welding aircraft parts.
From a previous life, I have unlimited certification for plate welding, high pressure steam pipe up to 24" in diameter and natural gas line up to 18" in diameter. I've set up the steam and gas lines in whole production plants, manufactured and erected the structural steel in buildings up to around 14 stories, plus done a bunch of custom ornamental iron work. I also have a patent on a product that's made from steel and concrete. It's been installed in buildings up and down the east coast from NH, to FL., Including at Fenway Park in Boston, MA...
You can do a lot with a welder!
Jim
About the TIG, I don't know if you have read every word of my thread of not, but the jist is I bought it for dirt cheap, sort of rebuilt the thing, wasn't happy enough... and due to my financial inability to buy a Supra as a college student, I needed to build something turbocharged.... So I found a YouTube video of a turbocharged LS400, I contacted him, and ever since he has been helping me out via email and excellent pictures, theory, and knowledge in general. I have heard that he is now a member so hopefully he can chime in sometime and say Hi because it is his build that I am truly copying with the help of a few over at Lextreme as well. Adam, feel free to say hi and add come criticism, and what not...
Anyways, the reason for the TIG is so I can create my own manifolds/charge piping/exhaust/etc. with out the need to have someone else do, cause as you know that welding talent/machinery is money in the bank. I want to weld aluminum, stainless, and mild.... and I am finding out it's quite difficult, however with time and practice, I am sure I will be laying the fish scales before too long.. I would love to have someone like you to have for experience, the guy who I buy my welding from from is pretty good, but he has no passion for autos. I would really like to do the whole pop can welding thing, that looks sweeeeet.....
The reason for the update.... just got done pulling one of the manifolds off to hack it up for the flanges and measure it for piping. Did I mention that it snowed 5 inches in the last 2 days? I had to shovel around the beat, but with a blanket, ratchet, 14mm, and a sawzall, I got it done in about 30 minutes. I decided to just cut the piping instead of trying to work with seized bolts under the car in the freezing weather. Since I am not reusing any of the old piping, I decided that it's not really worth to keep as Minnesota doesn't have emissions, I don't NEED cats.. However if a cop pulls me over, it's a nice little fix-it-ticket, but most don't spend the time to drop down and look, some carry mirrors, but most of the time they go after the big lifted trucks cause they can see it without having to get out of their cars. Blah, blah, blah right..? I know, pictures > words, I am going to get the show on the road... I shall get back to my cultural diversity lecture, good evening ladies and gents. Pictures to come next time I post, I promise, or I'll ban myself.
Last edited by 3UZFTE; 02-02-10 at 03:56 PM.
#154
Instructor
Thread Starter

As promised, here are some pictures of what I have so far. I decided that I would start the build and learn from trial and error, i.e. manifold height, runner length, etc, I don't plan on sticking with this manifold. Once I learn how to weld I will have much more input and knowhow to be able to put together a better piece. Anyways, I know my welding is terrible, I am getting it too hot, probably using too much filler but who cares, it's practice baby, practice... what you see is less than 10 hours of "helmet time". The hardest part I found is welding the 1-1/2" piping to the 1/2" mild, it's tough to learn the heating and feeding and circling and amperage control and rotation and distance and heat and.... It's a lot harder than you think people, but it's fun, I just wish I had a welding expert to teach me.
Since I no longer need the driver side cat, it was melted anyways due to the power steering fluid, I cut off the flange to save some time. This will connect to the driver side header to start my union.
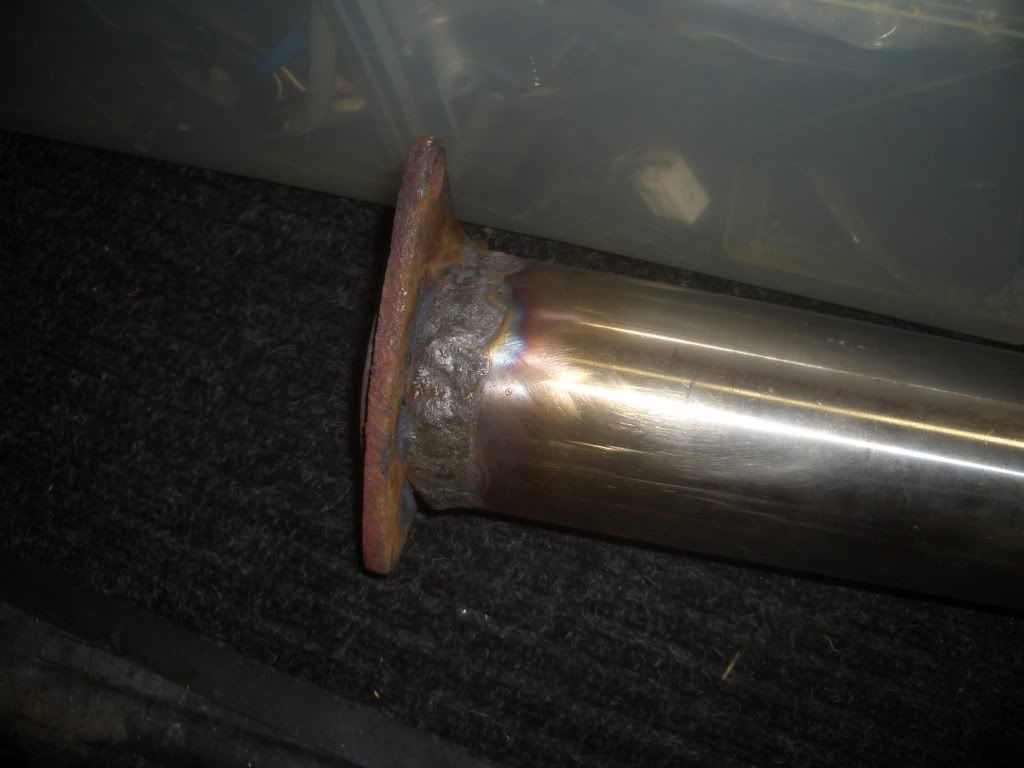
Everything tacked up, ready to weld up.
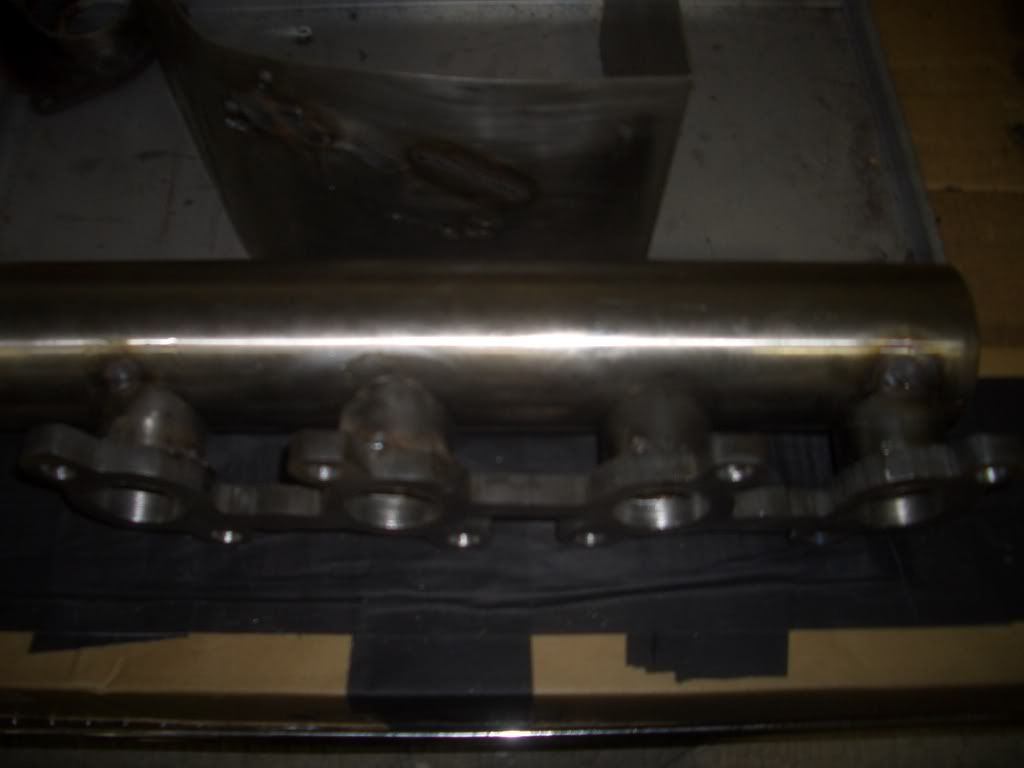
Runners will be ground out with my die grinder once I get everything welded up solid.
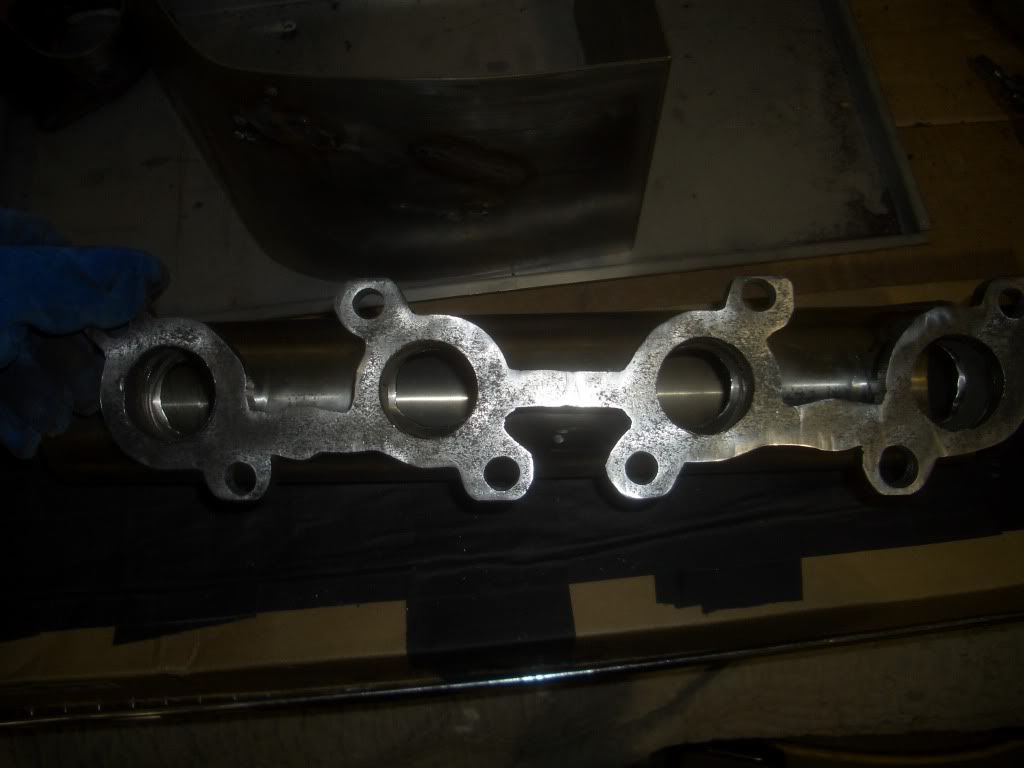
I weld like crap, again practice makes perfect, I am just doing this to get the ball rolling. I can start with other junk, I don't want to get bogged down on something that can be done better next time.
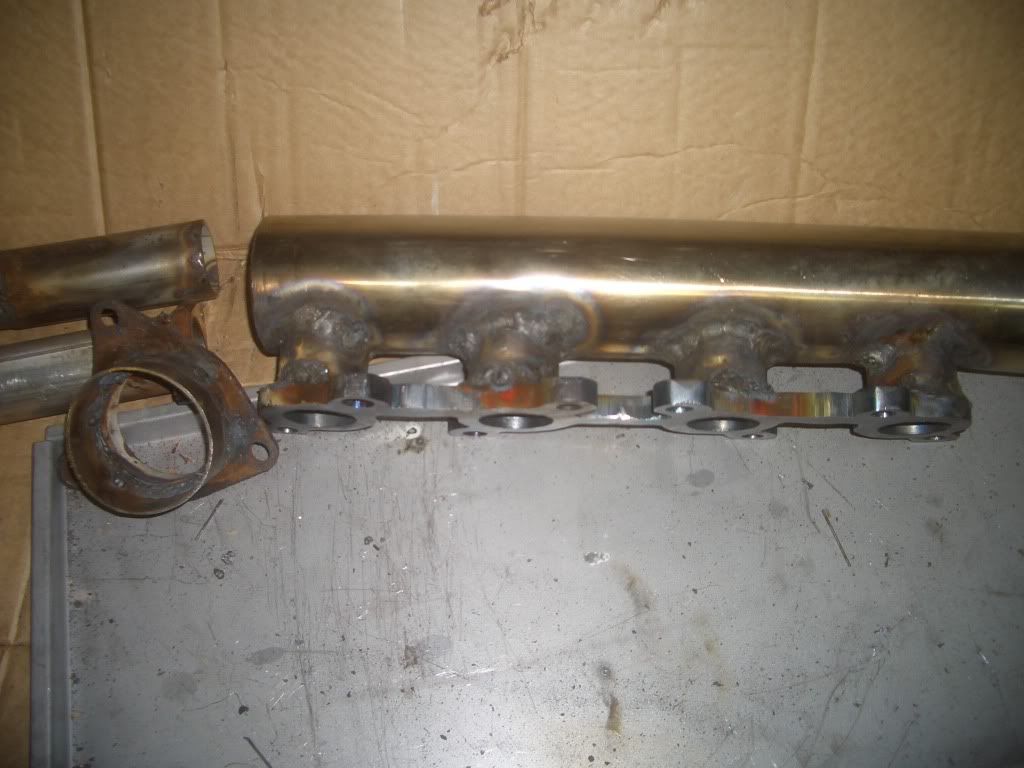
On a side note, I got crazy with photoshop because I was bored at a buddy's house. What do you guys think of the single tip exhaust if you fill in the hole that is left... I am going for the Supra look, I just want to run one 3" pipe turbo back and use 3" cat and muffler... Anyways... have a little laugh.
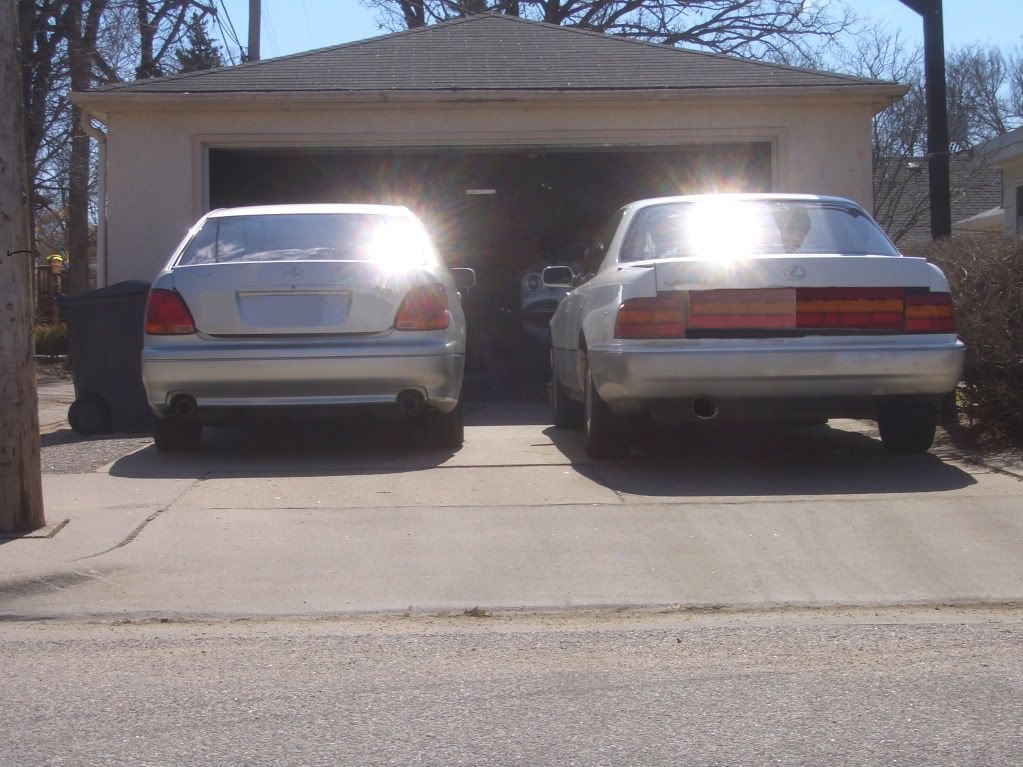
As always, feel free to say what you please... If it's about my welding, I know, I suck.
Since I no longer need the driver side cat, it was melted anyways due to the power steering fluid, I cut off the flange to save some time. This will connect to the driver side header to start my union.
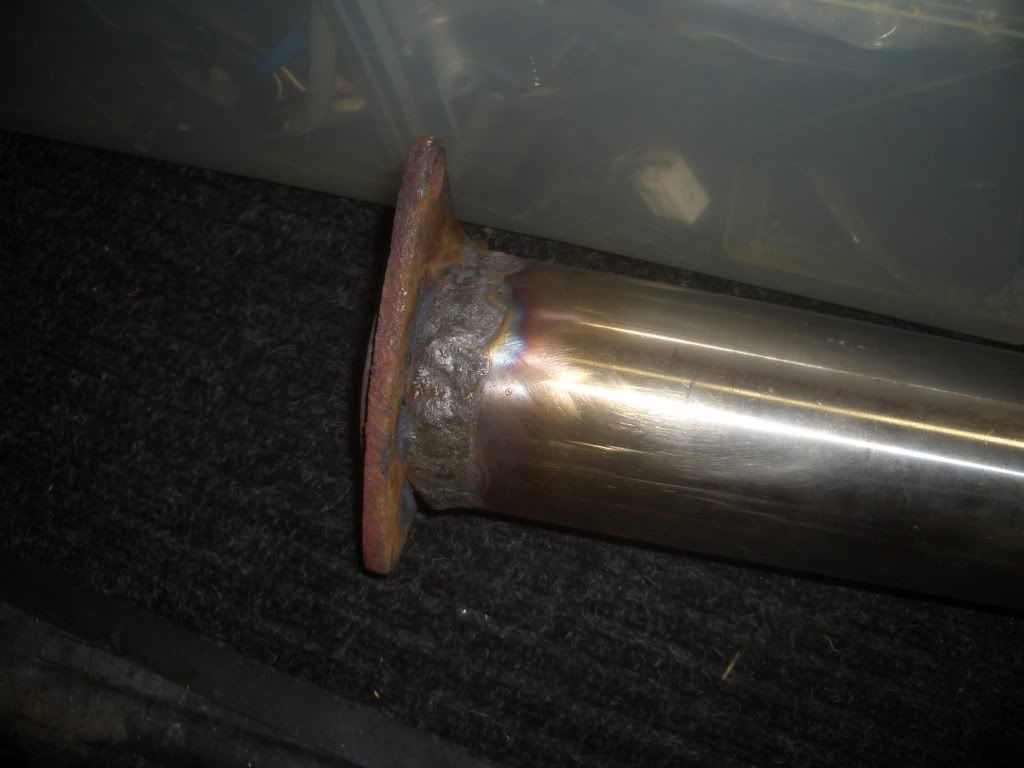
Everything tacked up, ready to weld up.
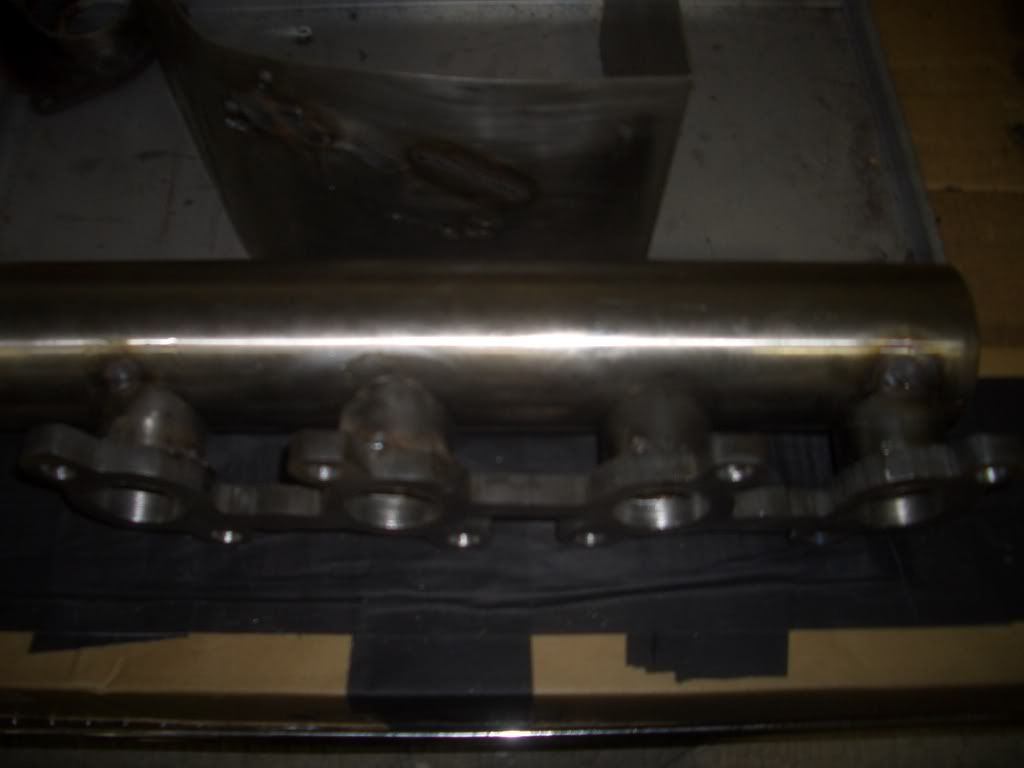
Runners will be ground out with my die grinder once I get everything welded up solid.
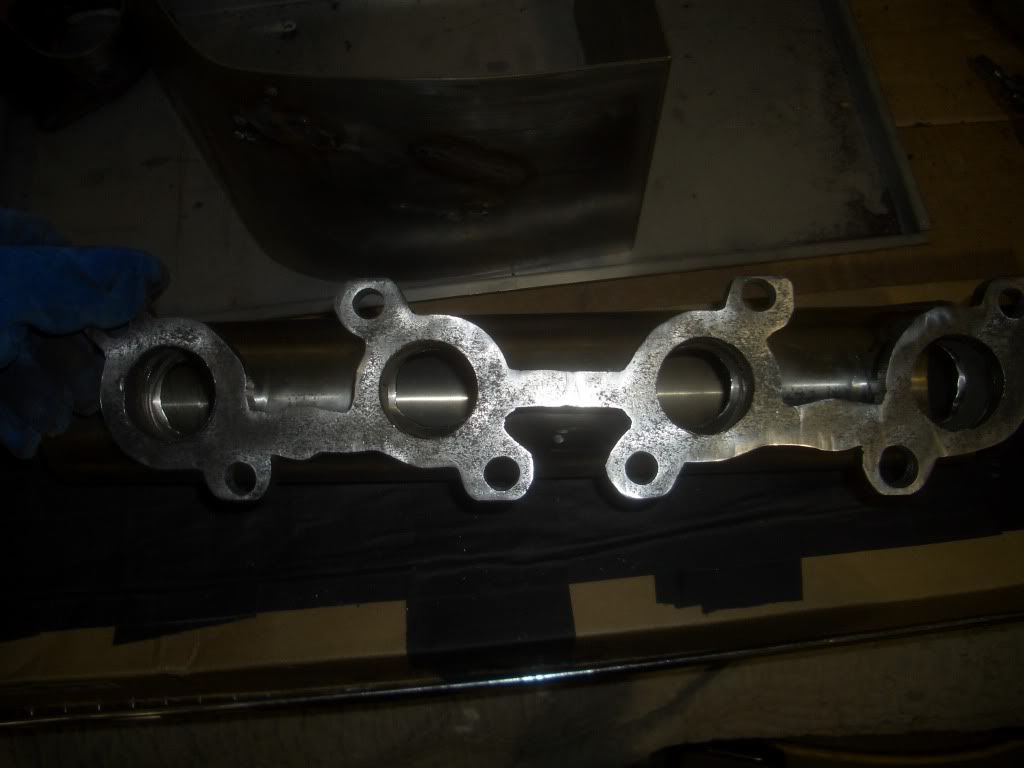
I weld like crap, again practice makes perfect, I am just doing this to get the ball rolling. I can start with other junk, I don't want to get bogged down on something that can be done better next time.
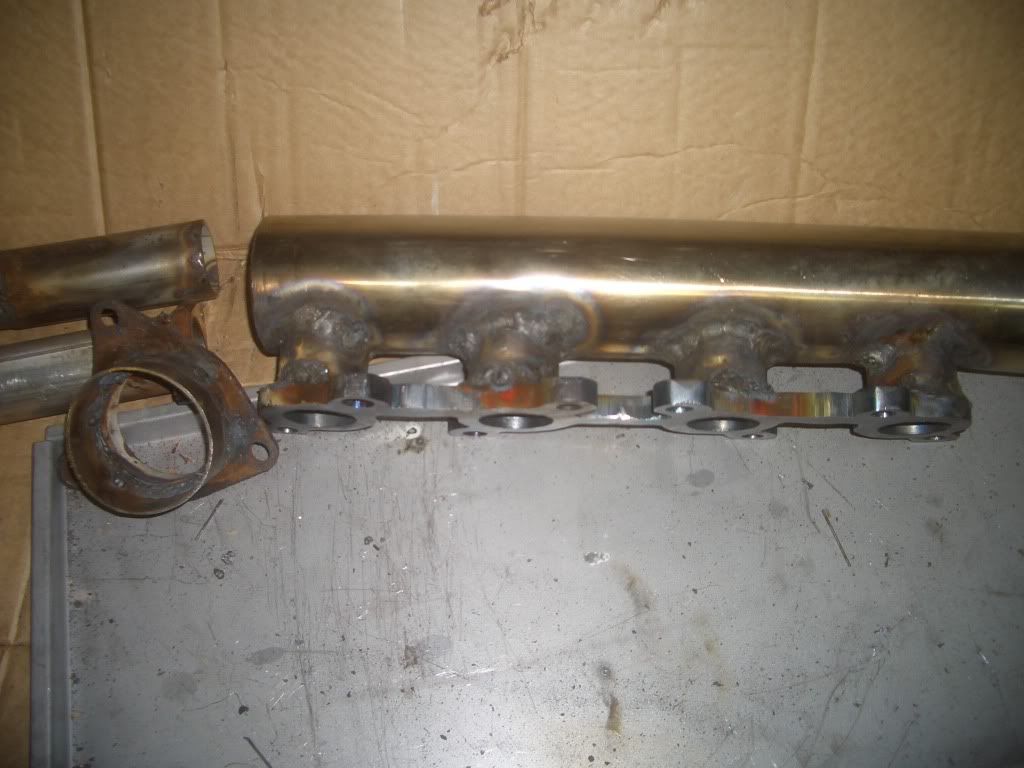
On a side note, I got crazy with photoshop because I was bored at a buddy's house. What do you guys think of the single tip exhaust if you fill in the hole that is left... I am going for the Supra look, I just want to run one 3" pipe turbo back and use 3" cat and muffler... Anyways... have a little laugh.
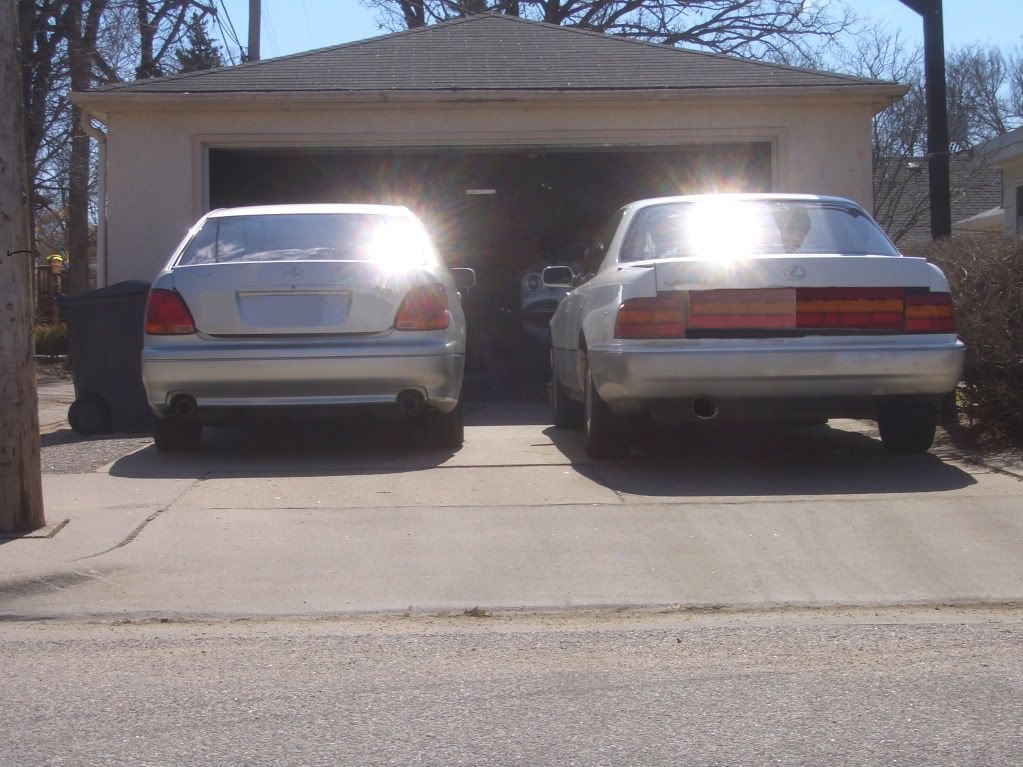
As always, feel free to say what you please... If it's about my welding, I know, I suck.
Last edited by 3UZFTE; 02-03-10 at 10:57 PM.
#155

Although $400 is a good price for any car, not sure if you can ever bring it back to a decent car to drive. 
It is too bad that a Lexus has been so mistreated over the years. With just a little bit of effort the car could have been kept up.
I bought a 1993 400LS over a year ago for $4500 that was in almost mint condition, just one speaker not working and the driver's seat wouldn't recline.
I thought that was a steal since the Blue book value was around $6000.
Good luck!

It is too bad that a Lexus has been so mistreated over the years. With just a little bit of effort the car could have been kept up.
I bought a 1993 400LS over a year ago for $4500 that was in almost mint condition, just one speaker not working and the driver's seat wouldn't recline.
I thought that was a steal since the Blue book value was around $6000.
Good luck!

#156
Driver School Candidate
Join Date: Dec 2009
Location: AZ
Posts: 25
Likes: 0
Received 0 Likes
on
0 Posts

Judging from the first pic it looks like you may have a great deal of arc wander. That will really make it difficult to weld. It happens when your tungsten is improperly sharpened or the tungsten is contaminated. Gas settings can also contribute to arc wander by blowing your puddle around. Any time you stick your tungsten or get any basemetal or filler rod on your tungsten you gotta re-grind the tip or you will have a mess on your hands. Also most of your time should be spent fitting pipe, if you can keep the gaps under 0.040in it will be much easyier. I know fitting pipe to those tollerances is a lot of work but it will be worth it, and after a while you get used to it and it becomes easy. Also welds should never have that much scale, you are either too hot or your gas is set too high or too low, it could also be that the bead was so wide that the sheilding was insufficent, however the soloution to that is not a bigger cup it is narrower beads. On that 3" stainless tube your bead should be between 3/16" to 1/4" wide, tops. And a #6 cup is plenty for that. Just remember to take it slow, that is one of the many advantages to TIG. You may want to learn to master the sweat bead before you start doing welds with filler. Just keep practicing, you'll get there.

#157
Driver School Candidate
Join Date: Jan 2010
Location: Texas
Posts: 2
Likes: 0
Received 0 Likes
on
0 Posts

Is there enough room to swap the factory manifolds side to side? That way they would point down & to the front and you could build a y pipe leading to the turbo off that. I've been thinking about doing this to my '92 but I haven't torn into anything yet.
#158
Instructor
Thread Starter

Judging from the first pic it looks like you may have a great deal of arc wander. That will really make it difficult to weld. It happens when your tungsten is improperly sharpened or the tungsten is contaminated. Gas settings can also contribute to arc wander by blowing your puddle around. Any time you stick your tungsten or get any basemetal or filler rod on your tungsten you gotta re-grind the tip or you will have a mess on your hands. Also most of your time should be spent fitting pipe, if you can keep the gaps under 0.040in it will be much easyier. I know fitting pipe to those tollerances is a lot of work but it will be worth it, and after a while you get used to it and it becomes easy. Also welds should never have that much scale, you are either too hot or your gas is set too high or too low, it could also be that the bead was so wide that the sheilding was insufficent, however the soloution to that is not a bigger cup it is narrower beads. On that 3" stainless tube your bead should be between 3/16" to 1/4" wide, tops. And a #6 cup is plenty for that. Just remember to take it slow, that is one of the many advantages to TIG. You may want to learn to master the sweat bead before you start doing welds with filler. Just keep practicing, you'll get there.

I didn't really look into it as I wasn't really a fan of having all my hot pipes in front of the motor when I can just keep the existing setup and make a manifold and turbo up-pipe and kill 2 birds with one stone. If you do a little searching, I am sure you'll find your answer.
Last edited by 3UZFTE; 02-07-10 at 06:22 PM.
#160
Driver School Candidate
Join Date: Dec 2009
Location: AZ
Posts: 25
Likes: 0
Received 0 Likes
on
0 Posts

You will have much better results using all stainless. Sometimes depending on the quality of the mild steel you are TIG welding you can run into a lot of problems with contamination. In my experience this happens a lot less frequently with stainless steel. Did you use a plasma cutter to make those flanges.
#161
Instructor
Thread Starter

^^^ If you guy's haven't already, check out e57820's signature, it is the reason why I am building this.
Instead of paying someone to bend my exhaust or buy bends, I decided I would try the wagiri construction, or pie cuts. I am getting better at this whole "helmet time", but if anyone has ever said it is easy, or you have thought it was easy, guess again. my plans are to have the hot side of the turbo, headers, crossover, and turbo footprint before spring rolls around. Here are my 90* bends made from 3 pieces. Yeah it would have been easier to pay someone to bend it, but I'd rather learn from trial and error and actually make some passes. Anyways, here are the "bends", I have started to grind them down, they need some more work, but it's a start.
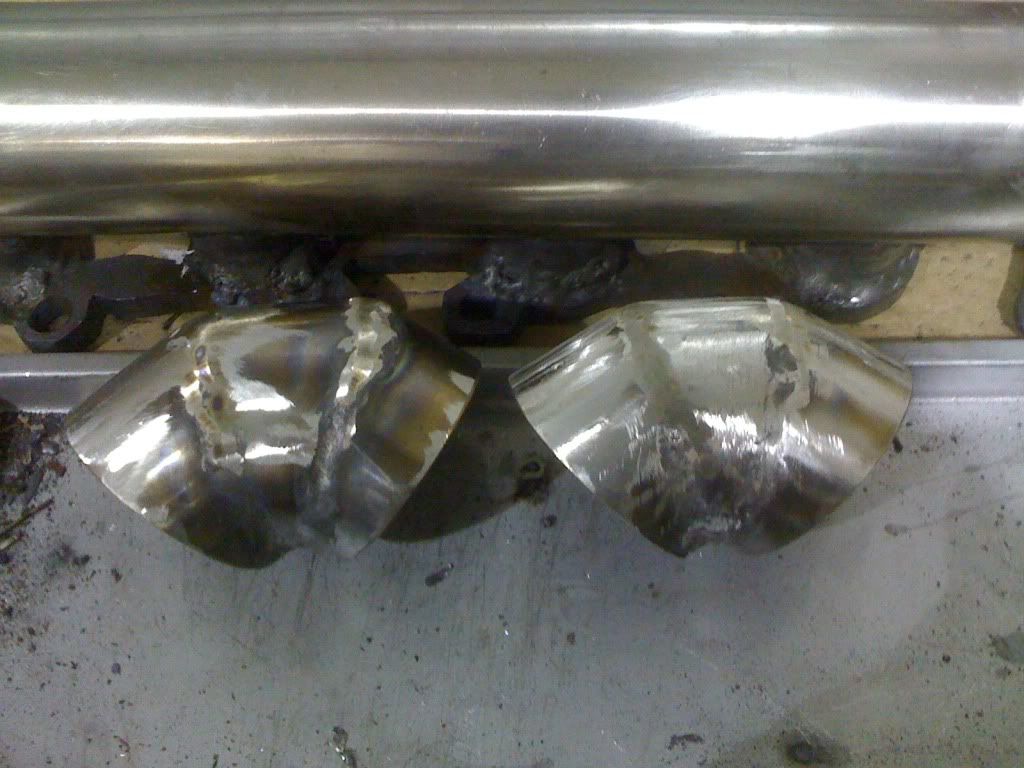
Thanks for coming by, hope your enjoying the build, I know I am.
Instead of paying someone to bend my exhaust or buy bends, I decided I would try the wagiri construction, or pie cuts. I am getting better at this whole "helmet time", but if anyone has ever said it is easy, or you have thought it was easy, guess again. my plans are to have the hot side of the turbo, headers, crossover, and turbo footprint before spring rolls around. Here are my 90* bends made from 3 pieces. Yeah it would have been easier to pay someone to bend it, but I'd rather learn from trial and error and actually make some passes. Anyways, here are the "bends", I have started to grind them down, they need some more work, but it's a start.
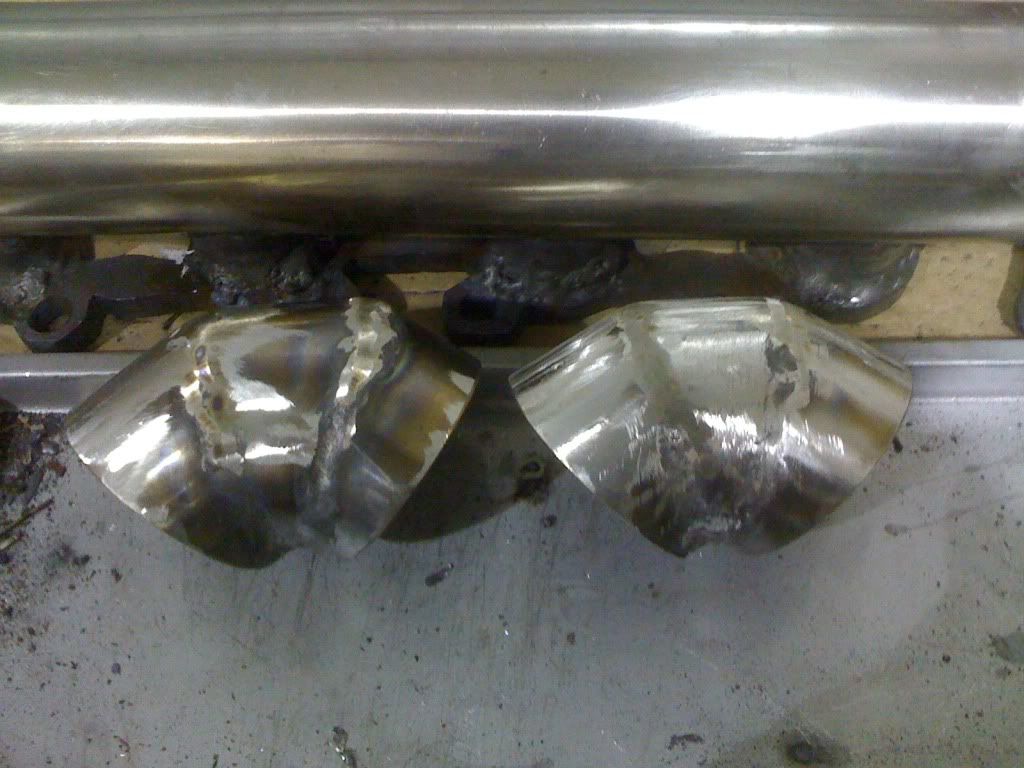
Thanks for coming by, hope your enjoying the build, I know I am.
#163
Instructor
Thread Starter

Hey e57820 and everyone else... I, for the longest, have been wondering how to tackle the power steering. So.. I decided that I didn't need to reinvent the wheel since I have been cruising a few other Toyota forums, I found a little easier, I think, way of doing this. At school, we have some engines just sitting on engine stands waiting to be built/rebuilt by student entering the auto program. I moseyed my way over there and saw that there were tons of Toyota engines, since we specialized in Toyota. I started peeking around, and sure enough I found this fitting I have been trying to find on the Supraforums for the longest. It appears to be the exact size as the LS4 fitting, but instead has a outlet instead of a reservoir.
I would like to note that IF I HAD the chance to do it over again, since I bought the SC400 pump instead of the LS400, I would've simply used the SC outlet as it allows a remote resv. as opposed to the LS outlet.
Here is the SC400 outlet...
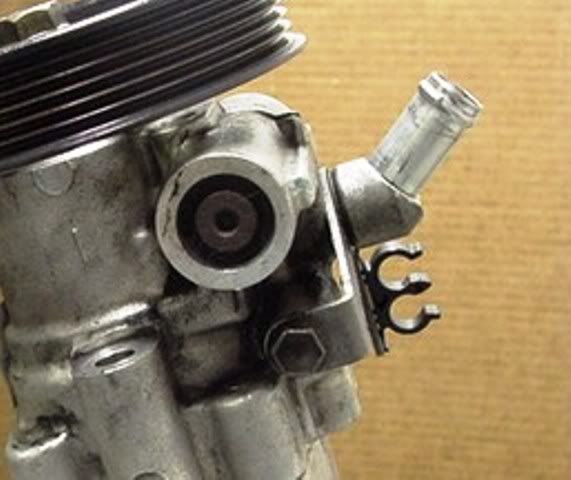
Here is the LS400 outlet...

Here is what I picked up...
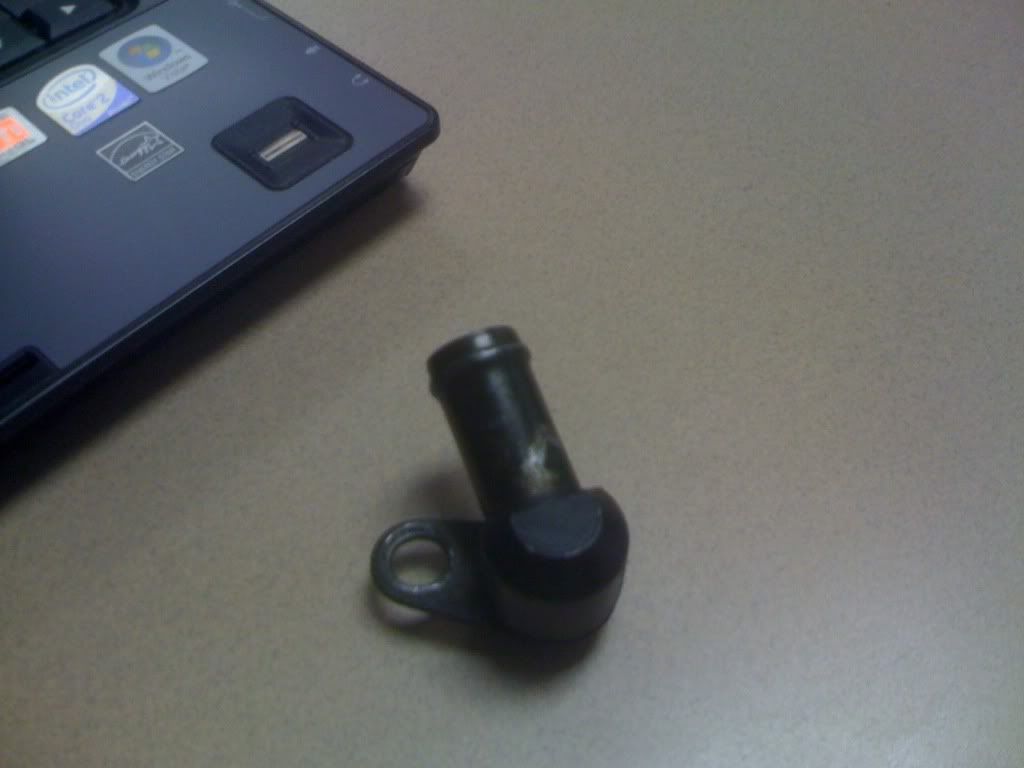
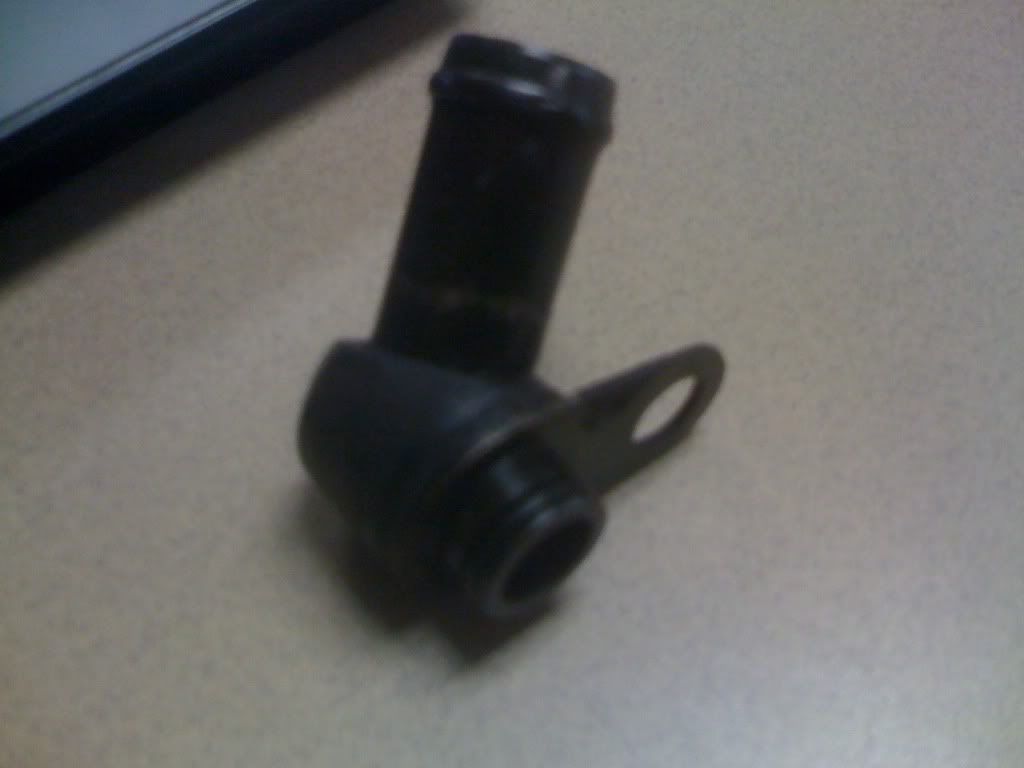
I will make my own bracket, I was thinking about welding it directly to the pump, but since my pump is a little greasy and I am not good as welding aluminum, I will just figure out how to bolt it down and use a nice and chunky o-ring.
Here are a few pictures of it in the pump, sorry for the poor quality, it's an iPhone picture while holding a flashlight in my other hand, and the hood with my head.
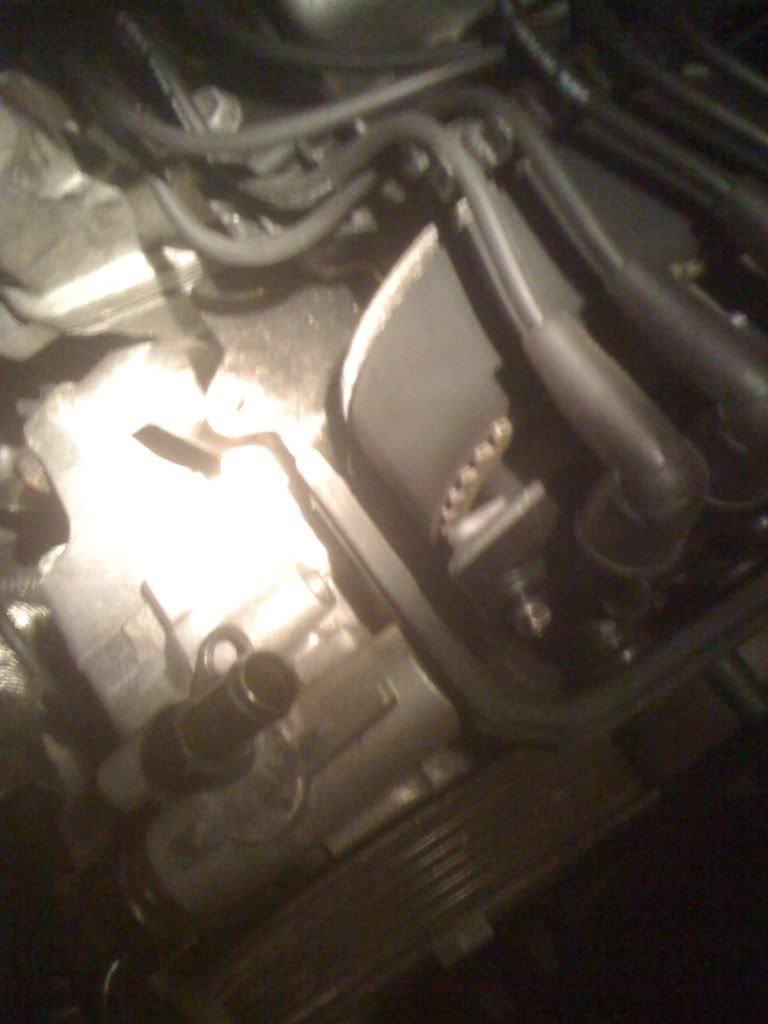
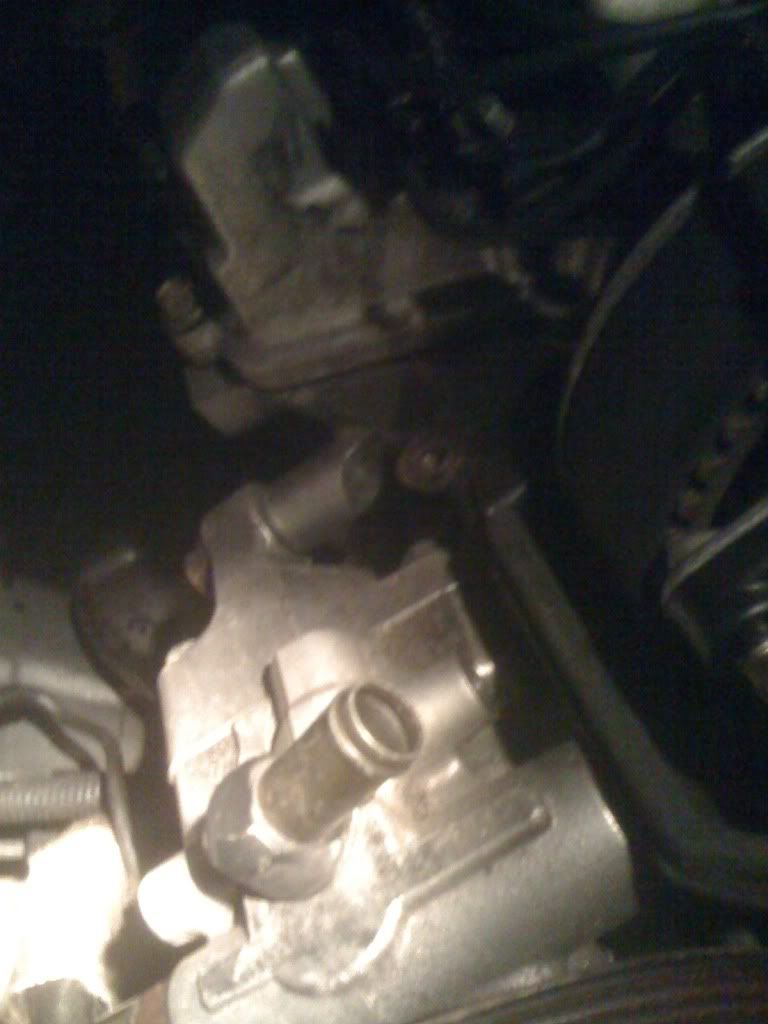
Any questions?
I would like to note that IF I HAD the chance to do it over again, since I bought the SC400 pump instead of the LS400, I would've simply used the SC outlet as it allows a remote resv. as opposed to the LS outlet.
Here is the SC400 outlet...
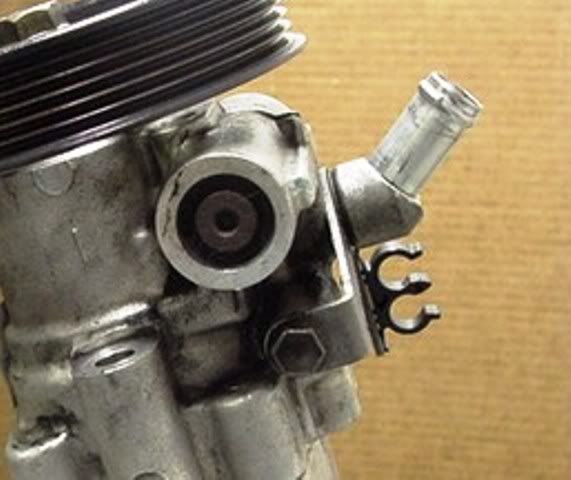
Here is the LS400 outlet...

Here is what I picked up...
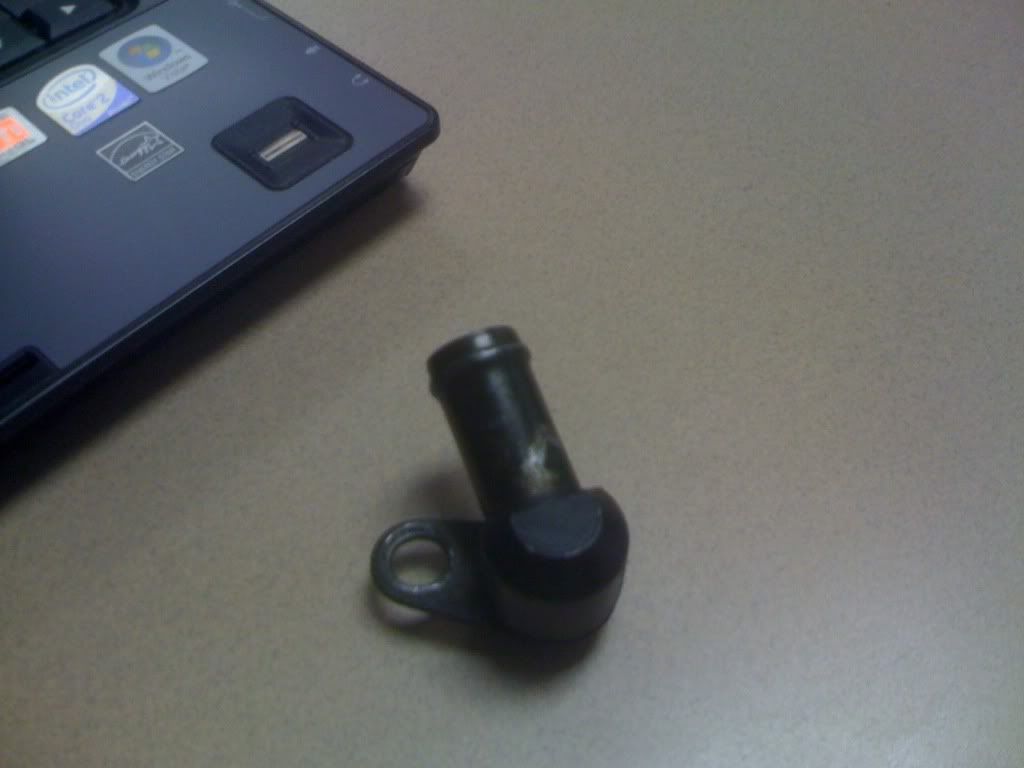
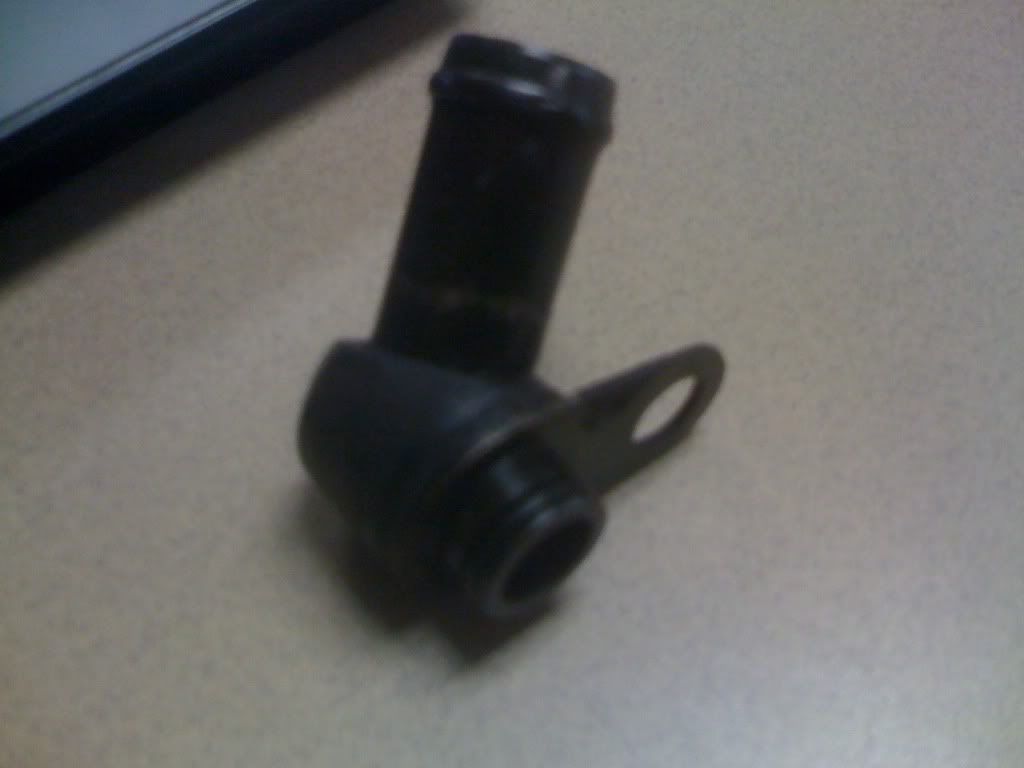
I will make my own bracket, I was thinking about welding it directly to the pump, but since my pump is a little greasy and I am not good as welding aluminum, I will just figure out how to bolt it down and use a nice and chunky o-ring.
Here are a few pictures of it in the pump, sorry for the poor quality, it's an iPhone picture while holding a flashlight in my other hand, and the hood with my head.
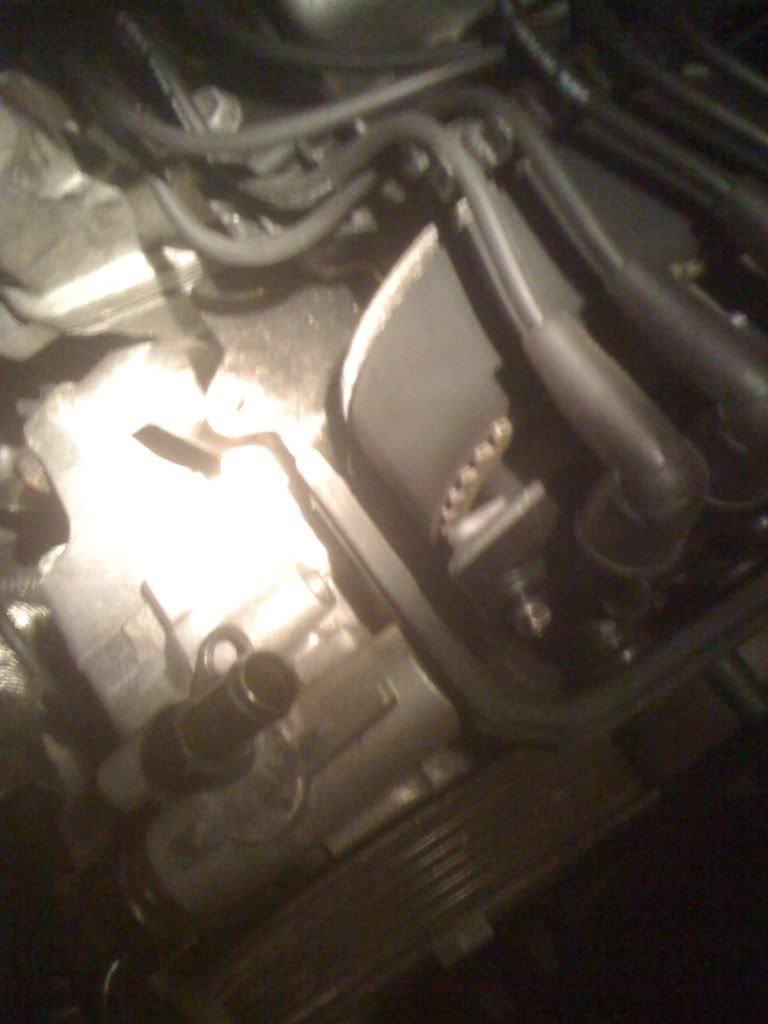
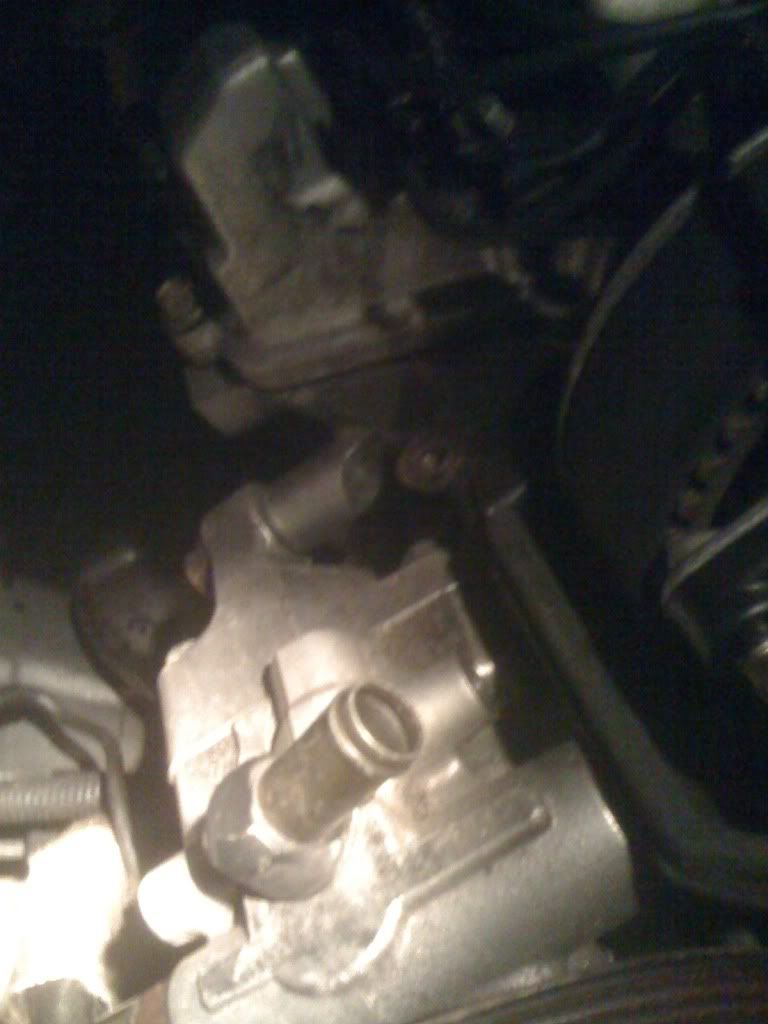
Any questions?
Last edited by 3UZFTE; 02-25-10 at 05:15 PM.